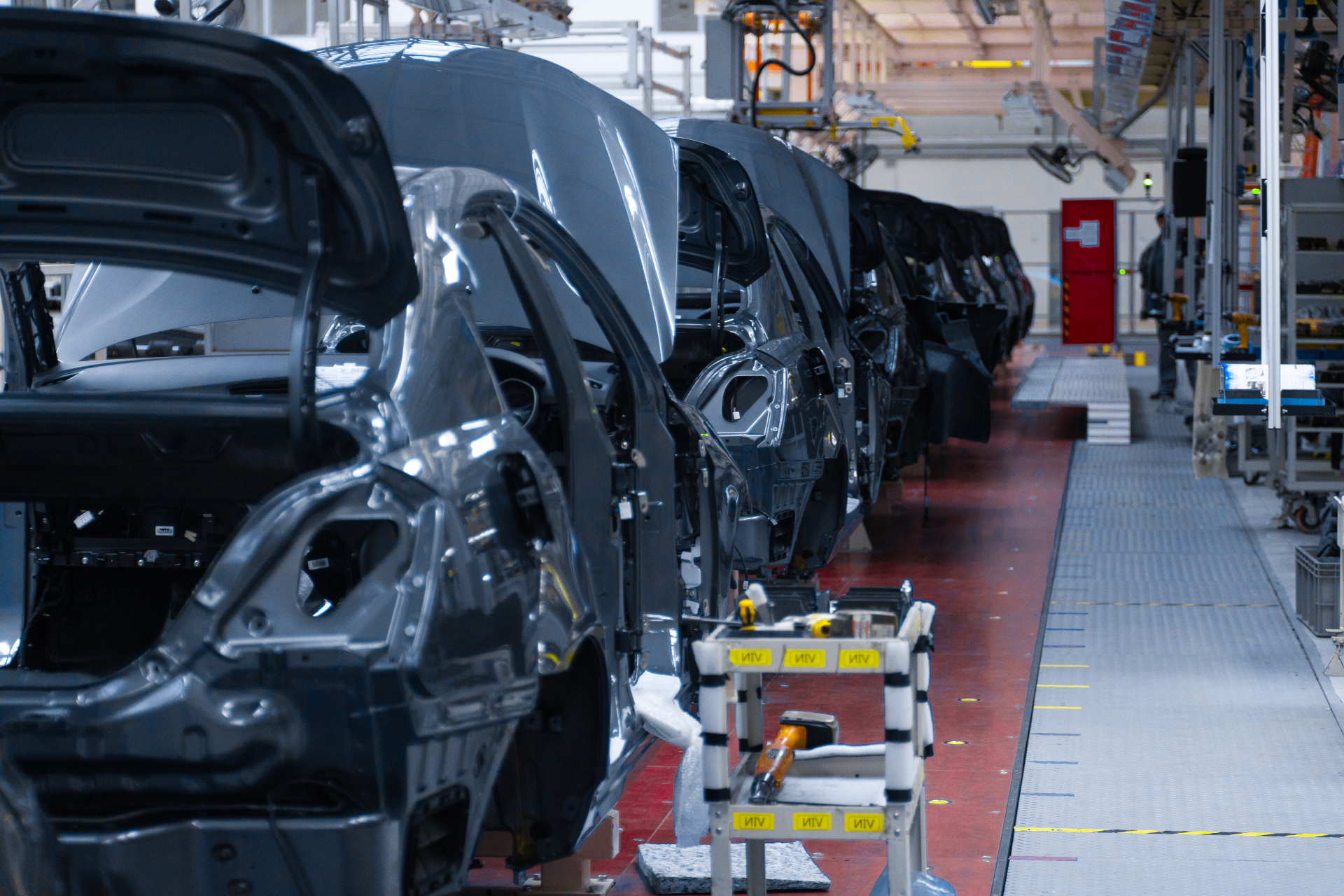
Контроль качества в процессе производства автомобилей включает в себя различные этапы и методы. Все они нужны для того, чтобы обеспечить безопасность для водителей и пассажиров.
Например, при создании автомобилей Lexus каждый сотрудник сборочного цеха играет роль инспектора. На этапах сборки все сотрудники знают о персональной ответственности, которую они несут за качество своей работы. При создании автомобилей проводят более 3100 различных проверок, в ходе которых специалисты тщательно осматривают автомобиль, тестируют системы, проверяют размеры, чтобы дать финальное заключение о том, соответствует ли результат норме и пройдена ли проверка.
Кроме этого, проводятся проверки готовых автомобилей. В том числе с использованием краш-тестов, которые мы часто видим в роликах в социальных сетях - когда автомобиль врезается в препятствия. Такие проверки помогают обнаружить дефекты в системе безопасности и изменить конструкцию авто таким образом, чтобы снизить риски для жизни и здоровья водителя и пассажира.
В статье расскажем о методах и этапах контроля качества на автомобильных заводах, а также поделимся полезными чек-листами, которые могут помочь автоматизировать процесс контроля.
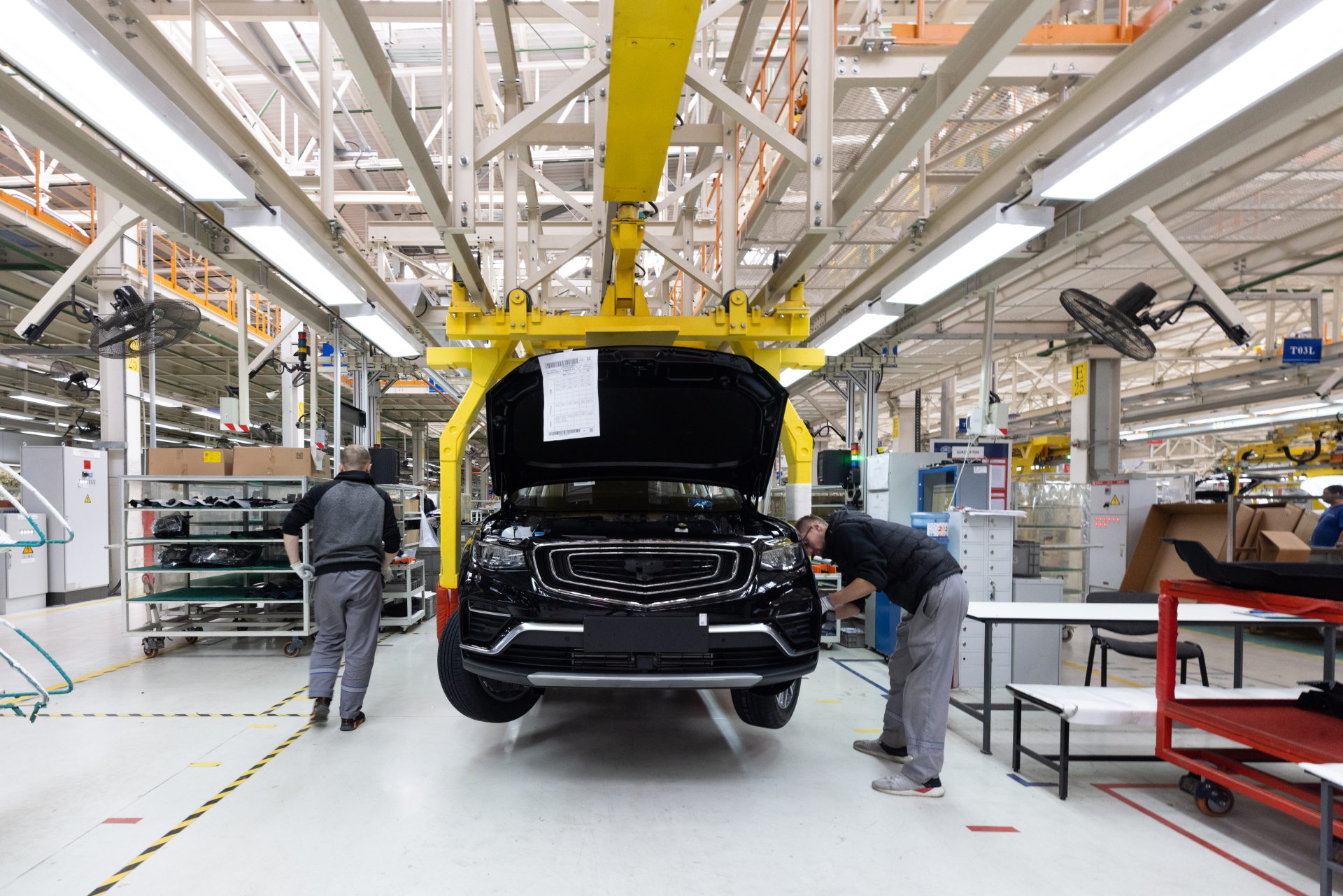
Методы контроля качества
Визуальный осмотр. Специалисты осматривают детали, узлы и готовые автомобили на наличие видимых дефектов, таких как царапины, вмятины, трещины и другие повреждения. Этот метод применяется на всех этапах производства, начиная с входного контроля материалов и заканчивая финальным осмотром готовых автомобилей.
Например, на производстве автомобилей Lexus контролеры качества покраски проходят регулярную аттестацию до 4 раз в год. Так проверяют остроту зрения, необходимую для выявления недостатков, которые они обязаны увидеть. Аттестация включает в себя в том числе тест на распознавание цветов: необходимо расположить ряд из 20 цветов в правильном порядке по спектру.
Неразрушающие методы контроля. Они нужны для того, чтобы проверять качество материалов и соединений без их разрушения. Они включают:
- Ультразвуковую дефектоскопию для выявления внутренних дефектов сварных швов.
- Рентгенографический контроль для обнаружения дефектов в металлических деталях.
- Магнитопорошковый метод для выявления дефектов в ферромагнитных материалах.
Испытания на прочность и долговечность. Автомобиль и его детали оценивают на способность выдерживать эксплуатационные нагрузки. Метод включает испытания на вибрацию и ударные нагрузки, тестирование на износ материалов, проверку стойкости к экстремальным температурам и другим агрессивным условиям.
Функциональные испытания. Проводятся для проверки работы всех систем автомобиля. Это могут быть тесты тормозной системы, проверка подвески, работы рулевого управления и других важных компонентов.
Основные этапы контроля качества на автомобильном заводе
Первый этап – это входной контроль. Здесь проверяются все материалы и комплектующие, которые поступают на завод. Цель – убедиться, что они соответствуют спецификациям и не содержат дефектов.
Проверка документации. Каждый материал или компонент, который поступает на завод, сопровождается документацией, в которой указаны его характеристики, производитель и результаты предварительных тестов. Специалисты по качеству проверяют эти документы.
Визуальный осмотр. Специалисты осматривают материалы и комплектующие на наличие видимых дефектов, таких как царапины, трещины, деформации или неправильная маркировка. Метод помогает выявить явные несоответствия.
Измерение и тестирование. Для точной оценки качества материалов и комплектующих используются измерительные инструменты и тесты. Например, металл может быть проверен на твердость, а пластиковые детали – на гибкость и устойчивость к механическим повреждениям. Электронные компоненты тестируются на работоспособность и соответствие электрическим характеристикам.
Неразрушающие методы контроля. Некоторые материалы и компоненты проверяют с помощью неразрушающих методов, таких как ультразвуковая дефектоскопия или рентгенографический контроль. Эти методы выявляют внутренние дефекты, которые не видны при обычном осмотре.
Сравнение с эталонами. Для некоторых комплектующих существуют эталонные образцы, с которыми сравниваются поступившие материалы.
Проверка условий хранения и транспортировки. Качество материалов и комплектующих может ухудшиться из-за неправильных условий хранения или транспортировки. Специалисты по качеству проверяют, чтобы все условия были соблюдены, и материалы не подвергались воздействию влаги, высоких температур или механических повреждений.
Отбор образцов для лабораторных испытаний. В некоторых случаях материалы отправляются в лабораторию, где проводятся углубленные тесты и анализы.
Например, при сборке машин Volvo в сборочных инструкциях прописаны последовательность и порядок выполнения операций, приведены контрольные карты, в которых прописано, что и как нужно контролировать. После выполнения каждой операции работник подписывает контрольный лист. Так проверяют работу операторов, заполнение документации, исправность оборудования.
Применение чек-листов или контрольных листов - эффективный способ проверять качество деталей и работу сотрудников. Чтобы автоматизировать этот процесс, можно использовать сервис электронных чек-листов CheckOffice.
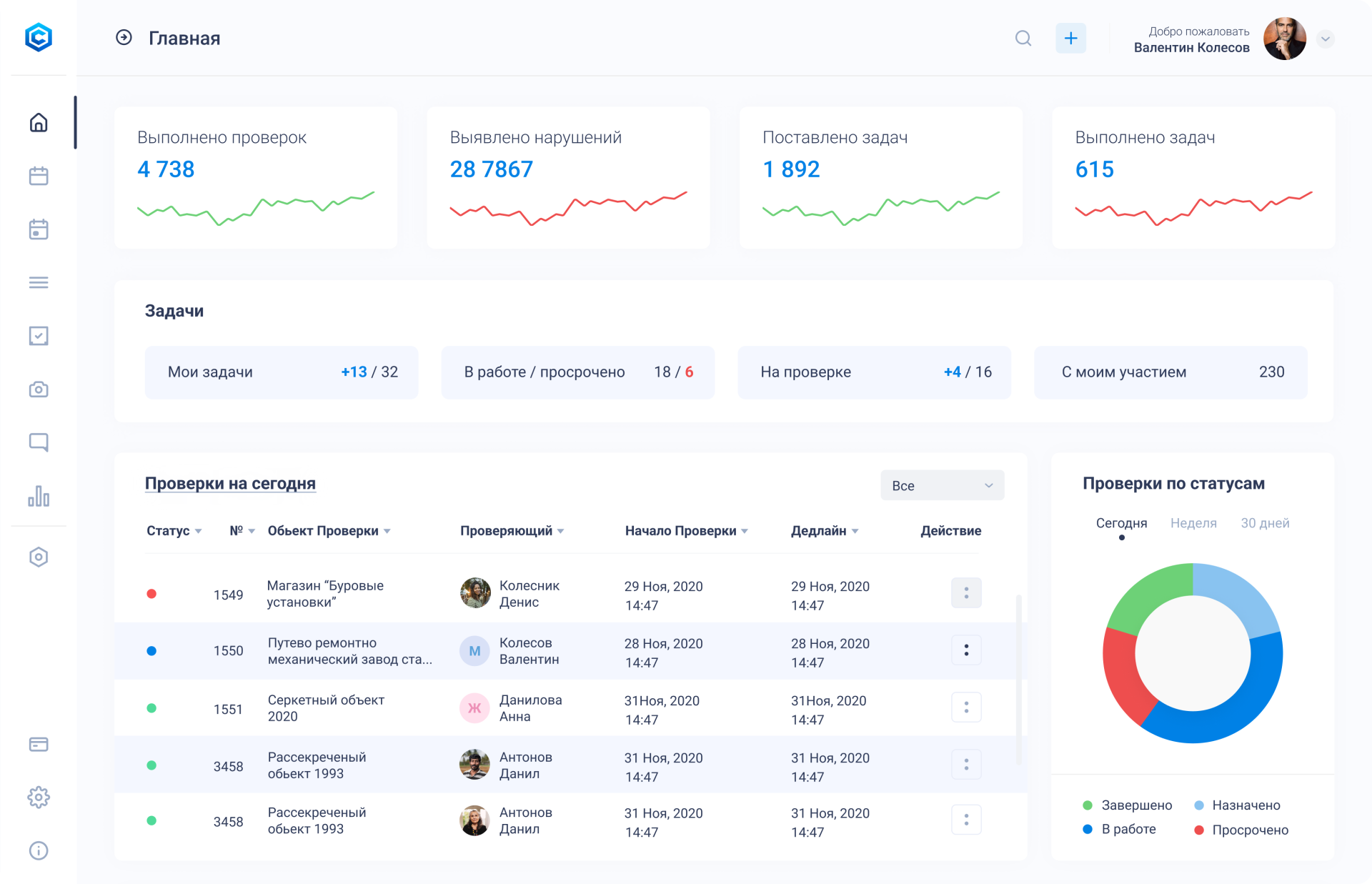
- Экономия времени. Процесс создания и заполнения электронного чек-листа достаточно быстрый, а полученные результаты будут сразу отправлены в личный кабинет ответственного сотрудника.
- Достоверность данных. При заполнении электронных чек-листов можно добавить вложения: фото или видео, текстовый комментарий, поставить подпись или приложить аудиозапись. Это минимизирует влияние человеческого фактора.
- Возможность анализировать данные. Собранные в результате проверок данные автоматически формируются в таблицы и графики, чтобы сделать восприятие информации простым и наглядным.
Далее идет контроль в процессе производства. На этом этапе следят за качеством выполнения каждой операции. Например, проверяют, насколько качественно сварен и собран кузов, правильно ли нанесена краска, и как установлены узлы и агрегаты.
Контроль сварки и сборки кузова. Используются визуальные осмотры и неразрушающие методы контроля, такие как ультразвуковая дефектоскопия, чтобы выявить любые дефекты или несоответствия. Геометрия кузова проверяется с помощью измерительных инструментов, чтобы убедиться, что он соответствует чертежам и спецификациям.
Контроль покраски. Качество покраски автомобиля важно для его внешнего вида и защиты от коррозии. Контроль включает проверку равномерности нанесения краски, её адгезии и толщины покрытия. Оценивается отсутствие дефектов: подтеков, пузырьков или пятен.
На заводах Volkswagen лакокрасочное покрытие проверяют на прочность: процарапывают его до пластика, обдают водяной струей под высоким давлением, а затем помещают в установку, именуемую гравилометром, где бомбардируют образцы металлической дробью.
Контроль сборки узлов и агрегатов. Проверяется правильность установки и функционирование основных узлов и агрегатов: двигателя, трансмиссии, подвески и систем управления. Используются автоматизированные системы, которые могут выявлять любые отклонения. Например, двигатель проверяют на специальных стендах, чтобы убедиться в его корректной работе и соответствии характеристикам.
Контроль качества сборки интерьера. Внутренние элементы автомобиля также проходят проверку на соответствие стандартам качества. Специалисты проверяют правильность установки, функциональность всех механизмов и отсутствие дефектов материалов.
На производстве автомобилей Volkswagen есть особые тесты на контакт с косметикой. Например, на кнопки стеклоподъемников наносят крем для рук и оставляют на сутки при температуре +80°С. Косметика не должна оставить следы. Рядом стоят лампы различной температуры, под которыми оценивается качество лакокрасочного покрытия – при любом освещении различий быть не должно.
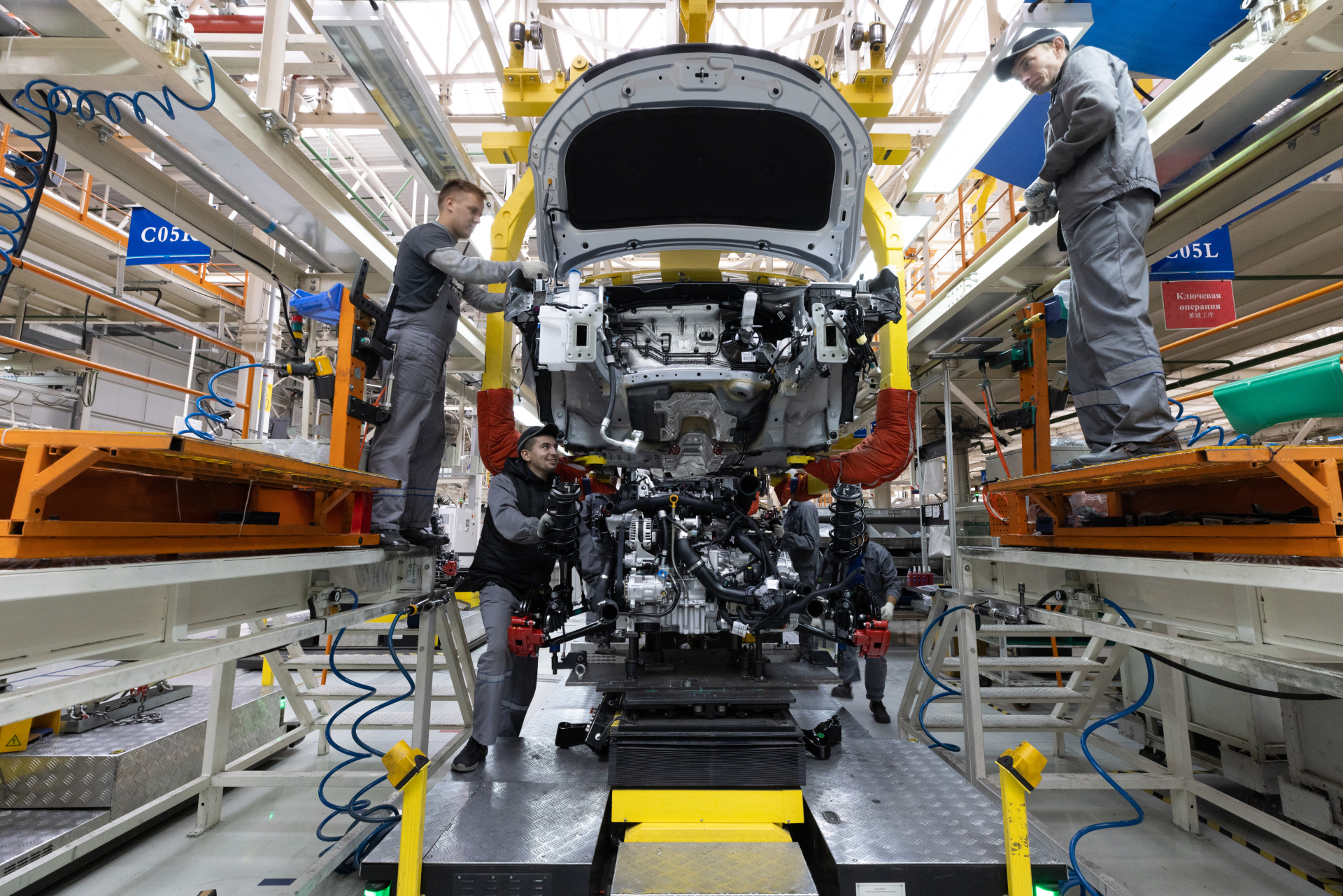
Функциональный контроль – следующий этап. Здесь проверяются все системы автомобиля, чтобы убедиться, что они работают правильно. Двигатель проверяют на мощность и уровень выбросов, электронные системы – на корректную работу, а тормоза и подвеску – на эффективность в условиях, имитирующих реальные дорожные условия.
Проверка двигателя. На специальных стендах проверяется мощность двигателя, уровень выбросов и работа систем впрыска топлива. Также проводятся тесты на устойчивость к различным условиям эксплуатации, таким как работа при высоких и низких температурах, под нагрузкой и на холостом ходу.
Тестирование тормозной системы. Тормоза также проверяются на испытательных стендах, где имитируются различные условия движения. Оценивается эффективность торможения, равномерность работы тормозных механизмов и их устойчивость к перегреву.
Проверка рулевого управления и подвески. Проверяется плавность и точность работы рулевого механизма, устойчивость автомобиля на дороге, работа амортизаторов и других элементов подвески. Эти тесты часто проводятся как на испытательных стендах, так и на специальных трассах.
Тестирование электронных систем. Современные автомобили оснащены системой управления двигателем, системами безопасности (ABS, ESP), климат-контролем, мультимедийной системой и так далее. Каждую из этих систем проверяют на корректность работы. Например, системы безопасности проверяют на быстрое и правильное срабатывание в различных условиях, а мультимедийные системы – на корректное воспроизведение аудио и видео, работу сенсорных экранов и навигации.
Проверка светотехники. Фары, задние фонари, поворотники и другие осветительные приборы проверяют на соответствие стандартам яркости, углов освещения и правильности работы.
Испытания на герметичность и шумоизоляцию. Тестируют способность автомобиля удерживать влагу и пыль снаружи, а также уровень звукоизоляции для комфорта водителя и пассажиров.
Проверка климатической системы. Климатическая система автомобиля (включая кондиционер и обогрев) проверяется на эффективность работы при различных температурных режимах. Оценивается способность системы быстро нагревать или охлаждать салон до комфортной температуры и поддерживать её.
На производстве Камаз применяются «петли качества», которые включают четыре основные составляющие.
Петля качества №1 работает там, где создается продукт. Она подразумевает выполнение операций по стандартным операционным картам, приложениям к ним, а также соблюдение принципа «трех НЕ»: не бери дефектный продукт, не делай брак сам, не передавай брак потребителю.
Петля качества №2 исключает возможность перемещения дефектов на следующие операции.
Петля качества №3 заключается в проведении ежедневного выборочного аудита продукта и процессов изготовления деталей.
Петля качества №4 – это аудит качества готовых продуктов. Независимые аудиторы проверяют готовый продукт с точки зрения потребителя.
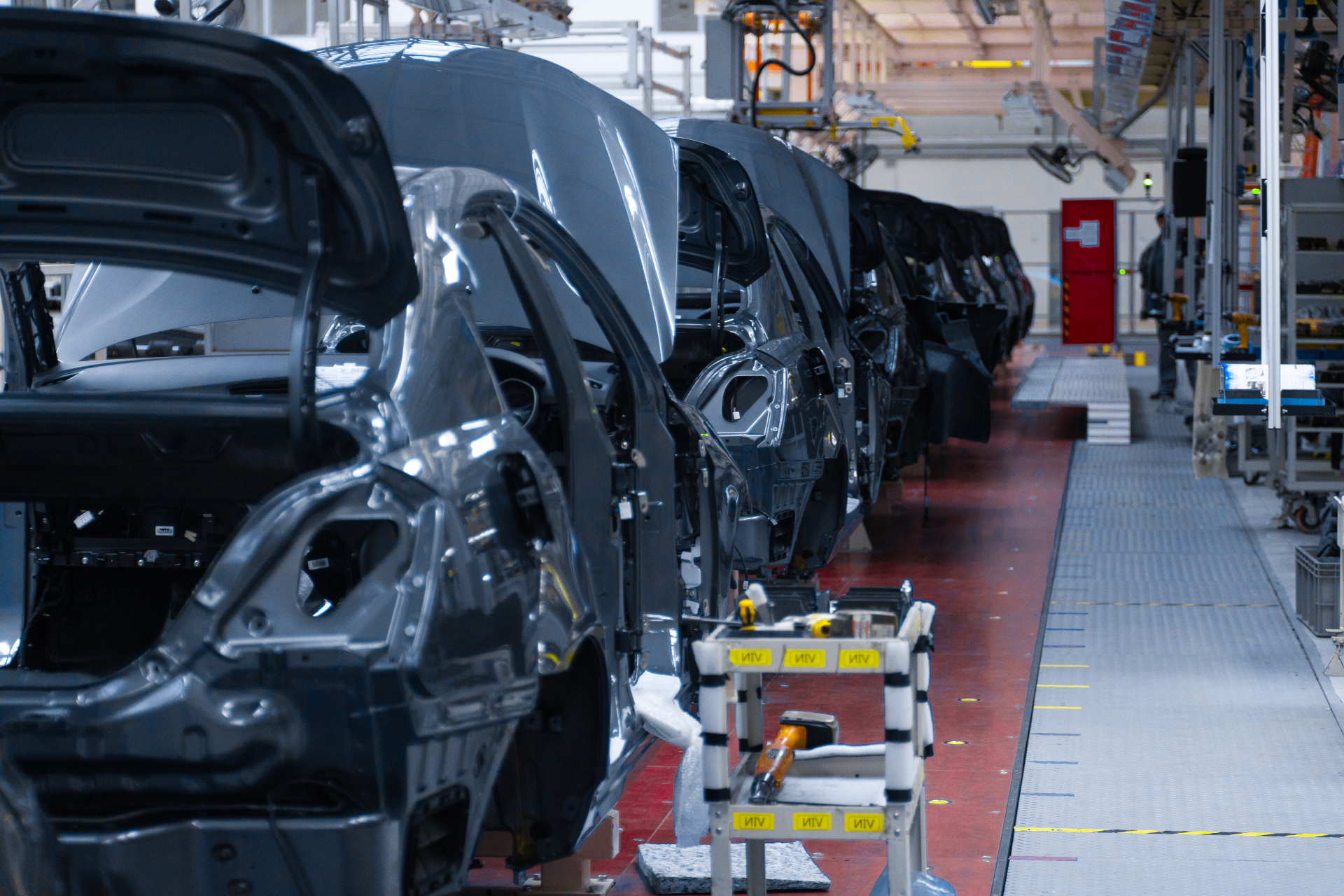
Финальный контроль качества на автомобильном заводе – это заключительный этап перед выпуском автомобиля на рынок, который включает проверку всех систем и компонентов. Цель этого этапа – убедиться, что каждый автомобиль соответствует стандартам качества и готов к эксплуатации.
Полный осмотр автомобиля. На этом этапе проводится тщательный визуальный осмотр автомобиля как снаружи, так и внутри. Проверяется качество сборки, отсутствие царапин, вмятин и других дефектов на кузове, состояние интерьера – правильность установки сидений, панелей, обивки и других элементов.
Дорожные испытания. Автомобиль проходит тестирование на специальной трассе, где имитируются различные дорожные условия. Это позволяет проверить работу двигателя, трансмиссии, тормозной системы, подвески и рулевого управления в реальных условиях. Тестируются электронные системы: ABS, ESP и системы безопасности.
Калибровка и настройка. Проводят окончательные калибровки и настройки систем автомобиля, таких как система навигации, мультимедийная система, система помощи водителю.
Тестирование безопасности. Проверяются системы безопасности автомобиля: подушки безопасности, ремни безопасности, системы помощи при экстренном торможении и другие. Их тестируют на быстрое и правильное срабатывание в аварийных ситуациях.
Финальная проверка документов. Проверяется вся сопроводительная документация автомобиля, включая сертификаты соответствия, результаты предыдущих тестов и испытаний, документация по сборке и установке комплектующих.