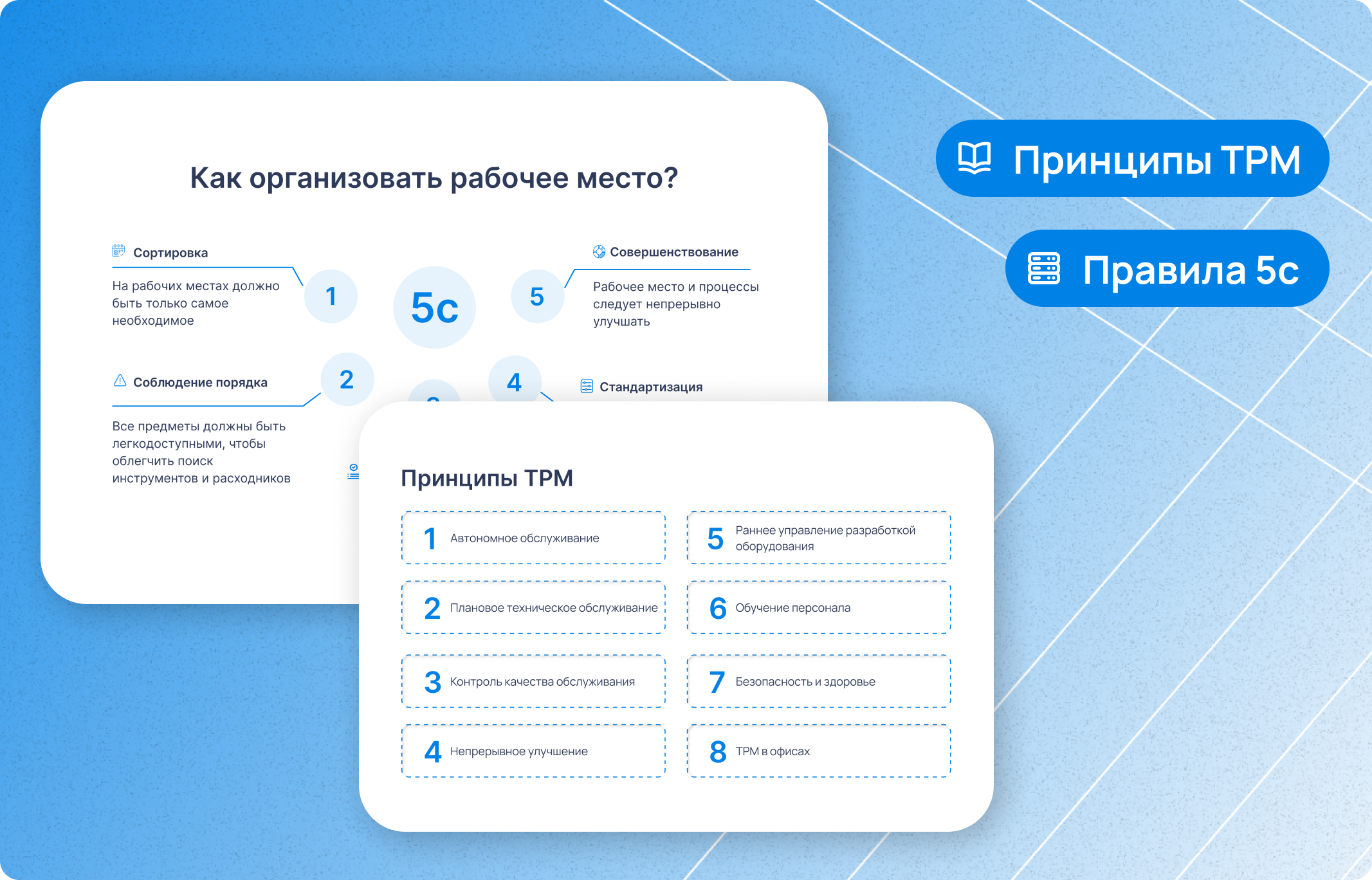
TPM (Total Productive Maintenance) — это комплексный подход к уходу за оборудованием. Его главная цель — увеличить срок службы оборудования и одновременно сократить возможные потери.
Чем система TPM отличается от традиционных подходов?
- Всеобщая ответственность. При традиционном подходе только сотрудники сервисной службы отвечают за исправную работу оборудования. В системе TPM в процесс вовлечены также линейные сотрудники. Они становятся источниками информации о состоянии оборудования и сами выполняют простейшие операции.
- Обслуживание по реальному состоянию. При традиционном подходе ремонт проводят планово, при этом текущее состояние оборудования не учитывается. В системе TPM во внимание берут реальную потребность в ремонте.
- Предупреждение поломок. Сотрудники проводят диагностику, изучают причины повторяющихся поломок и устраняют их. За счет этого оборудование работает бесперебойно.
Задача TPM
Главная задача ТРМ — устранить потери, которые снижают эффективность производства. К ним относятся:
-
Остановки работы из-за сбоев в работе оборудования, отказов, незапланированного обслуживания.
-
Настройки и переналадки, которые отнимают рабочее время.
-
Производственный брак из-за неправильных настроек или неисправностей.
TPM стремится устранить любые потери: паузы в работе, мелкие неисправности, брак производства и несчастные случаи, связанные с оборудованием.
Правило пяти «С»
Подход ТРМ основан на организации рабочих мест согласно правилам пяти «С».

- Сортировка. На рабочих местах должно быть только самое необходимое. Это позволяет не терять площади и не рассеивать внимание сотрудников.
- Содержание в чистоте. Чистое рабочее место помогает быстро понять источник сбоев в работе оборудования — подтеки, повреждения и так далее.
- Стандартизация. Важно создавать правила поддержания порядка на рабочих местах и инструкции, которые помогут эксплуатировать и обслуживать оборудование.
- Совершенствование. Рабочее место и процессы следует непрерывно улучшать.
Принципы TPM
Система TPM основана на нескольких принципах.
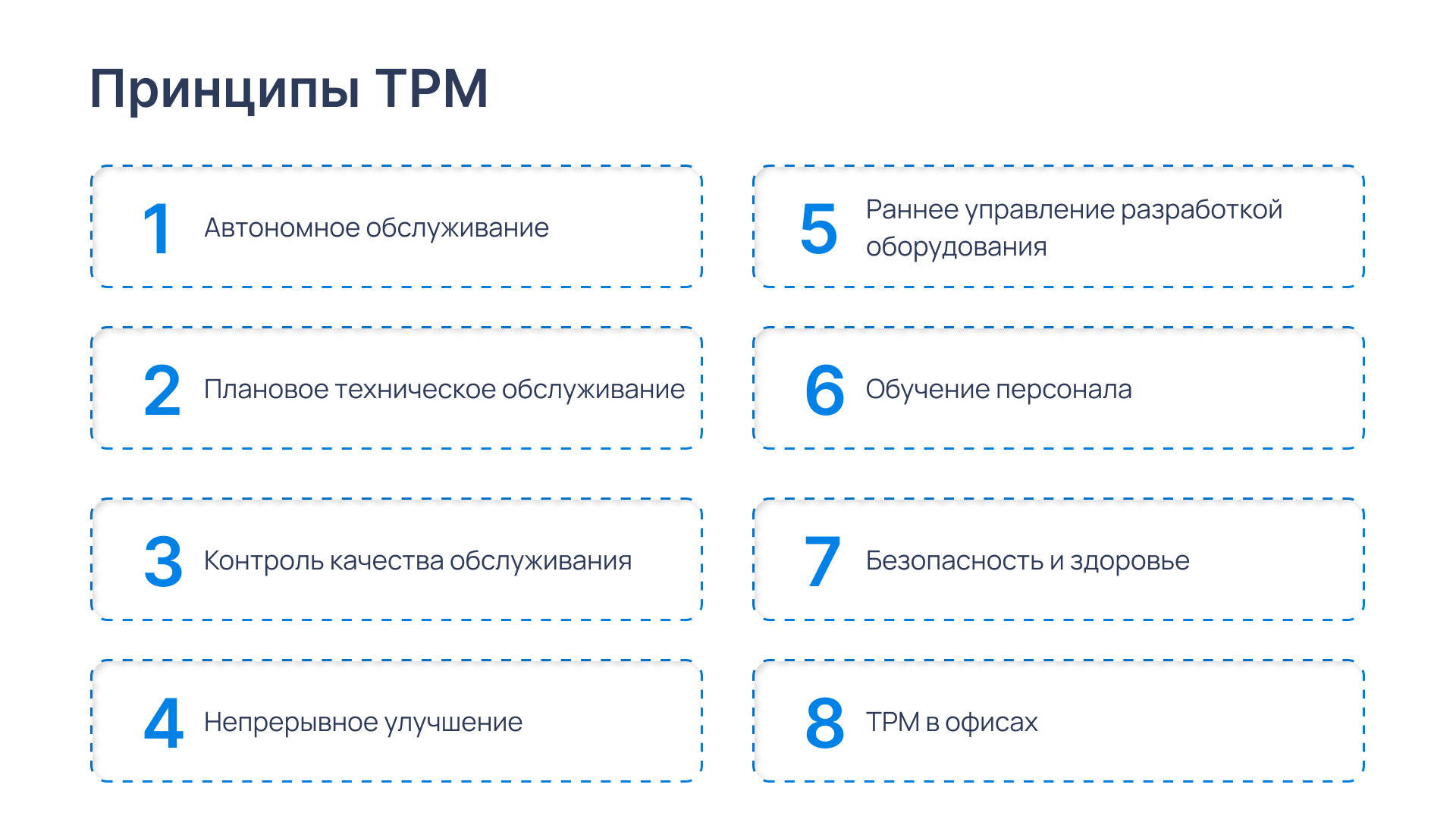
Автономное обслуживание
Автономное обслуживание — это принцип, согласно которому операторы оборудования берут на себя ответственность за его базовое обслуживание: регулярную чистку, смазку, регулировку и осмотр. Так появляется возможность увеличить срок службы оборудования и предотвратить поломки.
Возьмем пример из сферы производства деталей для автомобилей. Операторы на линии сборки двигателя выполняют ежедневные осмотры станков для выявления утечек масла и других проблем. Они регулярно очищают и смазывают оборудование - это предотвращает перегрев и износ деталей. Так сотрудники могут вовремя обнаруживать отклонения, например, шумы или вибрации, и избежать поломки оборудования в будущем.
Плановое техническое обслуживание
Плановое техническое обслуживание — это подход, при котором технические мероприятия по обслуживанию и ремонту выполняются по спланированному графику. Так сокращается количество аварийных простоев, повышается эффективность планирования ремонтных работ и закупки запчастей.
Например, на производстве деталей автомобиля есть график планового технического обслуживания станков. Раз в три месяца на каждом станке меняют изношенные штампы, проверяют системы и датчики. Это позволяет избежать аварийных поломок, которые могли бы привести к остановке всего производственного процесса.
Контроль качества обслуживания
Контроль качества обслуживания помогает предотвращать дефекты и поддерживать оборудования в исправном состоянии.
Читайте также: Менеджмент качества.
Так, на линии по производству коробок передач обнаружили, что после нескольких циклов сборки компоненты выходят из строя. Это приводило к отклонениям от стандартов качества. Проблема была регулярной, увеличивалось количество дефектов и остановок для калибровки и ремонта оборудования.
Сотрудники провели детальный анализ всех поломок. Выяснилось, что причиной сбоев была неправильная настройка датчиков на станке. Ремонт не решал корневую проблему, датчики постепенно выходили из строя из-за повышенной вибрации оборудования.
В результате приняли решение не только заменить датчики, но и установить дополнительные амортизаторы для уменьшения вибрации на всем станке. Количество дефектов резко снизилось, а оборудование стало работать стабильнее.
Непрерывное улучшение
Непрерывное улучшение — это постоянный процесс поиска и внедрения небольших изменений, которые постепенно приводят к значительным улучшениям.
На том же заводе по производству деталей заметили, что много времени тратится на переналадку оборудования при переходе от одной модели детали к другой.
Создали небольшую группу, в которую вошли операторы станков, мастера и представители отдела логистики. Вместе они проанализировали процесс и выяснили, что некоторые действия выполняются вручную и занимают больше времени, чем нужно.
Группа предложила создать чек-лист с четкими шагами переналадки оборудования и обучить операторов эффективным методам настройки станков. После внедрения этих изменений время переналадки сократилось.
Раннее управление разработкой оборудования
Суть принципа заключается в том, что опыт в обслуживании оборудования можно использовать для разработки машин следующего поколения.
Возьмем другой пример: фабрику по производству пластиковых бутылок. На заводе старое оборудование часто ломалось, а в процессе ремонта часто возникала одна и та же проблема - до некоторых деталей сложно добраться. Это приводило к долгим простоям, технический персонал тратил время на разбор оборудования.
Когда завод покупал новое оборудование, руководство привлекло инженеров и техников, которые обслуживали старые машины. Специалисты предложили выбрать оборудование с более удобным доступом к деталям, которые часто нуждаются в замене или чистке.
Обучение персонала
Специалисты, работающие с оборудованием, управленцы различных уровней проходят дополнительное обучение, которое помогает разобраться в особенностях устройств. Тогда самые простые задачи по обслуживанию оборудования можно делегировать линейному персоналу, мотивировать их не эксплуатировать оборудование на износ, а следить за увеличением срока эксплуатации.
На заводе по производству упаковочных материалов заметили, что операторы часто эксплуатируют оборудование на пределе возможностей, игнорируют регулярное обслуживание. Часто возникали поломки и потребность в ремонте.
Руководство завода организовало обучение операторов и линейных менеджеров. Во время курсов сотрудники узнали, как работает оборудование, на что обращать внимание для предотвращения поломок, как выполнять базовые задачи по техническому обслуживанию. Операторов обучили выявлять признаки возможных проблем, чтобы заранее сообщать о них техникам.
Безопасность и здоровье
Суть принципа - создать безопасные условия труда и снизить риски травм или аварий.
На заводе по производству автомобильных деталей на линиях часто возникали мелкие аварии и несчастные случаи из-за беспорядка. В рамках правил «5С» рабочие места были пересмотрены: ненужные инструменты убрали, оставшиеся организовали в удобные и безопасные зоны. Разработали четкие стандарты для уборки и поддержания порядка, которые выполняются ежедневно. В результате сократилось количество аварийных ситуаций, снизился риск травм, работать стало удобнее и безопаснее.
TPM в офисах
Похожие практики TPM можно использовать и для административного персонала в офисах.
Например, в офисе компании “Ромашка” сотрудники часто сталкивались с проблемой поиска нужных электронных файлов. Документы были разложены по разным папкам, каждый хранил их по-своему — возникала путаница.
Для решения этой проблемы в офисе решили внедрить принципы TPM. Сначала сотрудники договорились о стандартизации хранения файлов: создали единую систему папок с четкими названиями и категориями для всех документов. Файлы теперь хранятся в одной системе, к которой каждый имеет доступ. Ввели практику регулярной чистки — сотрудники ежемесячно удаляют или архивируют устаревшие файлы, чтобы не засорять рабочие папки. Время на поиск документов сократилось, а процесс работы стал более прозрачным и эффективным.
Система TPM и каждый из ее принципов важен для создания эффективной системы управления оборудованием и производственными процессами. Их использование помогает повышать производительность, снижать затраты и совершенствовать систему безопасности на предприятии.